External links now open in a new browser tab - turn this off in your UCP - Read more here.
Sbeckman7's Project: BR1
Update: Finishing up frame design and hopefully going to buy metal this weekend or the next. After much consideration I realized it would be most beneficial to outsourse the welding to a professional for a variety of reasons. First, the cost to benefit ratio seems in favor of paying a proffesional welder the amount it would take to buy a decent welder itself. Second, the fact that I am not an experienced welder means it wouldn't be smart for me to practice on something that I would ultimately be trusting my life with. Third, the smaller amount of time it would take for a proffessional to weld the frame would give me more time to work on assembling the car itself.
Alright, time for another update. I've been working on the frame design and have finished the floor. It will be lowered three inches below the main beams by sypporting tubing and triangulation for support. Here is a picture of the proposed design.
I will insert the picture into the post later but the school server won't let me use the normal website.
http://s1113.photobucket.com/albums/k51 ... rframe.jpg
I will insert the picture into the post later but the school server won't let me use the normal website.
http://s1113.photobucket.com/albums/k51 ... rframe.jpg
You know you can just type out [img]and[/img] instead of pressing the buttons, right?sbeckman7 wrote: I will insert the picture into the post later but the school server won't let me use the normal website.
It's looking better. What's the reason for the open rectangle in the center of the car?
I might make those rear diagonals into and X instead of a /. That would add more rigidity as well as additional protection in case of a side impact into a tire wall or another car.
tsmall07 wrote:You know you can just type out [img]and[/img] instead of pressing the buttons, right?sbeckman7 wrote: I will insert the picture into the post later but the school server won't let me use the normal website.
It's looking better. What's the reason for the open rectangle in the center of the car?
I might make those rear diagonals into and X instead of a /. That would add more rigidity as well as additional protection in case of a side impact into a tire wall or another car.
Yeah, even with the image functions it wouldnt post at school

-
- Posts: 10719
- Joined: Feb 12, 2006 12:00 PM
- Location: CHI, IL
Agree on the rear long diagonals being Xs. The center rectangle is the driveshaft/trans tunnel, no? Presumably that will be strengthened by having vertical walls and tying into the structure from the top somehow.tsmall07 wrote:You know you can just type out [img]and[/img] instead of pressing the buttons, right?sbeckman7 wrote: I will insert the picture into the post later but the school server won't let me use the normal website.
It's looking better. What's the reason for the open rectangle in the center of the car?
I might make those rear diagonals into and X instead of a /. That would add more rigidity as well as additional protection in case of a side impact into a tire wall or another car.
-tammer
I was thinking thans tunnel, too, but it looks like the f/r bars that make the rectangle look like they are at the same level as everything else. I would make sense if they were bent up to make a tunnel.
You can build an effective tunnel with square tubing if you don't think you can do the bends with the round. Just make sure it's essentially a trapezoid with no bottom.
You can build an effective tunnel with square tubing if you don't think you can do the bends with the round. Just make sure it's essentially a trapezoid with no bottom.
-
- Beamter
- Posts: 23035
- Joined: Apr 08, 2009 10:30 PM
- Location: Charlottesville, VA
- Contact:
Why? That seems odd to me. If it were me, I would put a drop in the frame itself @ the firewall and keep all the bracing in approximately the same plane as the frame. Then, take the frame back up in front of the rear suspension. That would also make it easier to have a flat bottom, which is better for aerodynamics.sbeckman7 wrote:the floor needs to be 3" lower than the rails
-
- Posts: 10719
- Joined: Feb 12, 2006 12:00 PM
- Location: CHI, IL
This, which also allows you to weld the bracing inside the frame around the full perimeter of the brace tubes.tsmall07 wrote:Why? That seems odd to me. If it were me, I would put a drop in the frame itself @ the firewall and keep all the bracing in approximately the same plane as the frame. Then, take the frame back up in front of the rear suspension. That would also make it easier to have a flat bottom, which is better for aerodynamics.sbeckman7 wrote:the floor needs to be 3" lower than the rails
-tammer
If you went with what we're saying, your frame profile would look like this:
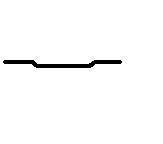
I've never seen a vehicle structure, custom or otherwise, that looks like the profile you've drawn above.
I've never seen a vehicle structure, custom or otherwise, that looks like the profile you've drawn above.
It would allow for a flat bottom, or bellypan. The underside of the car being flat is better for aerodynamics. I don't understand why this would change your seating position. You're building the car. Put the seat and pedals at whatever height you want. Frame configuration isn't really a factor here.sbeckman7 wrote: It also seems like it would make the floor more uneven, not flatter. I think I would end up sitting lower than the pedal box.
tsmall07 wrote:If you went with what we're saying, your frame profile would look like this:
I've never seen a vehicle structure, custom or otherwise, that looks like the profile you've drawn above.
It would allow for a flat bottom, or bellypan. The underside of the car being flat is better for aerodynamics. I don't understand why this would change your seating position. You're building the car. Put the seat and pedals at whatever height you want. Frame configuration isn't really a factor here.sbeckman7 wrote: It also seems like it would make the floor more uneven, not flatter. I think I would end up sitting lower than the pedal box.
Right, I get what you guys are saying. I just thought it would be worth more trouble than it's worth (although frankly I wouldn't know). If I went with my design, the floorpan would have the same underbody characteristics as the front half of your drawing; it wouldn't come back up before the rear subframe. If it would make sense to redo the main beams to the than I guess a small setback is worth it for added simplicity and strength. If I'm being stubborn it's because I'm told to redo the one thing that I have accomplished

sbeckman7 wrote: If I'm being stubborn it's because I'm told to redo the one thing that I have accomplished


We're not trying to design your car for you. Build it the way you think it should be a learn from it. It's easy to sit back in my arm chair and tell you how I would build it. I'm not doing it, though, you are!
By "beams" do you mean "frame rails"?sbeckman7 wrote:Alright, simple enough. So here's a question: would I only lower the part of the two beams that run parallel to one another?
start the drop in the frame before (towards the front of) the two diagonals that are not parallel. This looks like it would be just behind your engine mounts. You want all of your bracing to come into the frame rail, not below it. I think you will thank yourself later when you make the trans cross member, as well. Have you measured the height difference between the engine and trans mounts?
Now I see what you're saying. This looks like it will also help with mounting the control arms. As for finding the heights between engine and tranny mounts, I have yet to do that. I guess I'd either have to bolt the two together and look at it that way or get measurements off of a complete e28.
Do you think it would be wise to redo the frame rails after the top half of the frame (the stuff in progress on the second drawing) is completed? I'm thinking that way it will have more structure and be less likely to deform. Since the mounting points are still the same, it would only mean that I would have to wait to build the floor.
Do you think it would be wise to redo the frame rails after the top half of the frame (the stuff in progress on the second drawing) is completed? I'm thinking that way it will have more structure and be less likely to deform. Since the mounting points are still the same, it would only mean that I would have to wait to build the floor.
I suppose you can wait until the rest is done, but I'd just weld some temporary supports in while the cutting/rewelding is going on.
Word of advice for the future:
Never fully weld anything until you sure SURE that it won't have to move again. I would get your whole frame system together (with engine, trans, and diff mounts in place) with heavy tacks before you finish weld anything. Of course, you have to pay attention to accessibility with this method as you move forward.
Word of advice for the future:
Never fully weld anything until you sure SURE that it won't have to move again. I would get your whole frame system together (with engine, trans, and diff mounts in place) with heavy tacks before you finish weld anything. Of course, you have to pay attention to accessibility with this method as you move forward.
sounds good! And so a new direction begins...
A few quick little facts for everyone:
1. If this car weighs 1600lbs, a reasonable estimate, the stock 180 hp motor will give me 225hp/ton. My dream fully reworked 320+hp magical creation of Paul Burke would yield roughly 400hp/ton. Either way looks promising.
2. I emailed CARA Charities, an organization based in indianapolis which supports youth involvement in motorsports and driving programs, a proposal for a sponsorship. A call to their office this morning informed me that my email is currently being looked over. Fingers crossed.
3. I got into my first choice US college, IUPUI with the maximum academic scholarship! It's a branch of Purdue University located in Indianapolis (close to the CARA headquarters actually) and is the location of my future Motorsport Engineering School of Technology. I have reasons to be happy
4. Happy holidays/new years to everyone on here!

A few quick little facts for everyone:
1. If this car weighs 1600lbs, a reasonable estimate, the stock 180 hp motor will give me 225hp/ton. My dream fully reworked 320+hp magical creation of Paul Burke would yield roughly 400hp/ton. Either way looks promising.
2. I emailed CARA Charities, an organization based in indianapolis which supports youth involvement in motorsports and driving programs, a proposal for a sponsorship. A call to their office this morning informed me that my email is currently being looked over. Fingers crossed.
3. I got into my first choice US college, IUPUI with the maximum academic scholarship! It's a branch of Purdue University located in Indianapolis (close to the CARA headquarters actually) and is the location of my future Motorsport Engineering School of Technology. I have reasons to be happy

4. Happy holidays/new years to everyone on here!
So I decided to just jump into lowering the frame rails after all. Made two of the four pieces today, pics below. I'll eventually cut off the excess metal created from cutting at an angle and weld them shut. The 3 inch drop is within a 3 inch length so a 45 deg. angle did the trick and the pieces turned out very accurate. As to my problem regarding the control arm mounting points, I've outlined the proposed cutting area on the inside of the main frame to raise the arm to the proper height. It seems like a lot of metal to remove at a place as structural as this, but the other side of the rectangular pipe will need much less material removed due to the angle at which it mounts.
As it sits now:

Location of drop point:

Proposed cutting area: (sorry bout the picture)

As it sits now:

Location of drop point:

Proposed cutting area: (sorry bout the picture)

-
- Beamter
- Posts: 23035
- Joined: Apr 08, 2009 10:30 PM
- Location: Charlottesville, VA
- Contact: