Sbeckman7's Project: BR1
Update: Got the Koni's ordered, got the upper spring perches ordered, and am choosing between three pairs of seats for the pair I'm going to use. Contenders are the Corbeau Forza, Corbeau FX1 Pro, or a used set of Sparco Evo's, all for roughly the same price. The Forza doesnt seem to have as good lateral support as the FX1 but its a lot cheaper. And the Sparco's are, well, Sparco's. My friend got one for $100 and its really comfortable so we'll see. Another issue will be where the shoulder strap holes are in relation to the back of my head; I don't want to need a helmet on all the time just to stay comfortable. Won't be buying in the immediate future so I have time to think about it.
-
- Posts: 760
- Joined: Oct 19, 2010 9:03 PM
- Location: Bay Area
Thanks for the first hand experience information. I have decided to go with the Evo 2 Plus since there are currently some extremely good deals. $80 bucks away...E.rouzbeh.28 wrote:I would say to go with the Evo's. My friend has them in his car and they are surprisingly comfortable. I also drifted, done high speed turns, and just drag raced his car while sitting in those seats, and the support it gives is incredible.
-
- Posts: 2168
- Joined: Jul 27, 2009 12:43 PM
- Location: Houston, TX
Eh it would be an option if I didnt already have the 265 laying around. It came in the e28 parts car, so I'm just gonna use it. Plus I don't need 6 speeds, although it would be kinda cool. In other news, finished the left strut today! Welded the threaded collar back on and we're in business. Still looking for the threaded portion of the right side strut, but for now I don't need it so I will continue as usual. Going to ACE Hardware tomorrow to pick up some 1/4" steel plate to get started on the strut mounts. And some more good news: the setup sits lower than I originally thought, with the high point at about 30".
Since it's now spring break I've been able to spend more time with Daniel at his shop. I got the steel from OSH and we're about halfway through finishing the camber plates. I decided to make new ones out of steel instead of the aluminum ones supplied so I could weld them directly onto the frame. So far so good.

The heaviest thing you can get for $500 bucks

Daniel doing his thing


where we left off today


The heaviest thing you can get for $500 bucks

Daniel doing his thing


where we left off today

-
- Posts: 253
- Joined: Mar 18, 2011 7:23 PM
- Location: San Francisco
-
- Posts: 10719
- Joined: Feb 12, 2006 12:00 PM
- Location: CHI, IL
Reattached the other strut housing today since there is no need to have it separated anymore. The right side strut still needs the threaded bit of the housing welded back on but that wont stop me from rolling the car home if I don't have it by the end of the school year. The metal shop I've been using wanted to charge me about $10/foot for 1.5" x .120" DOM tubing so I'm ordering it online instead. Hopefully I'll be ordering the metal for the suspension reinforcement this week if I can scrape the cash together.




Last edited by sbeckman7 on Apr 25, 2011 6:53 PM, edited 1 time in total.
-
- Beamter
- Posts: 23035
- Joined: Apr 08, 2009 10:30 PM
- Location: Charlottesville, VA
- Contact:
Thank you for the idea. I'm planning a simple jig using a strut brace and some suppport beams that will hold the camber plates at the correct angle and spacing. Since I have nothing better to do I've also started on the floor. Designing transmission tunnel to attach onto roll bar in the rear of the car (I previously had no idea of where it would terminate in the back). That's about it for now as I'm just waiting for metal. Oh, and I got the green light to be able to enroll in autoshop classes at the community college over the summer and next year from Purdue. 750il, where are you...mooseheadm5 wrote:You need to make a reference jig from an E28 to relate the position of the tabs to the position of the subframe.
Today was more of the same: dimensions and planning. I have confirmation that the roll bar will be here by the weekend. Haven't drawn the transmission tunnel in yet because I am unsure of how it will tie in with the upper half of the frame at the moment, although the "Locost 7's" have been a good reference. I also constructed a temporary stand for the pedals to get an idea of how high they would have to be mounted and look for any clearance issues.







will be copying this transmission tunnel
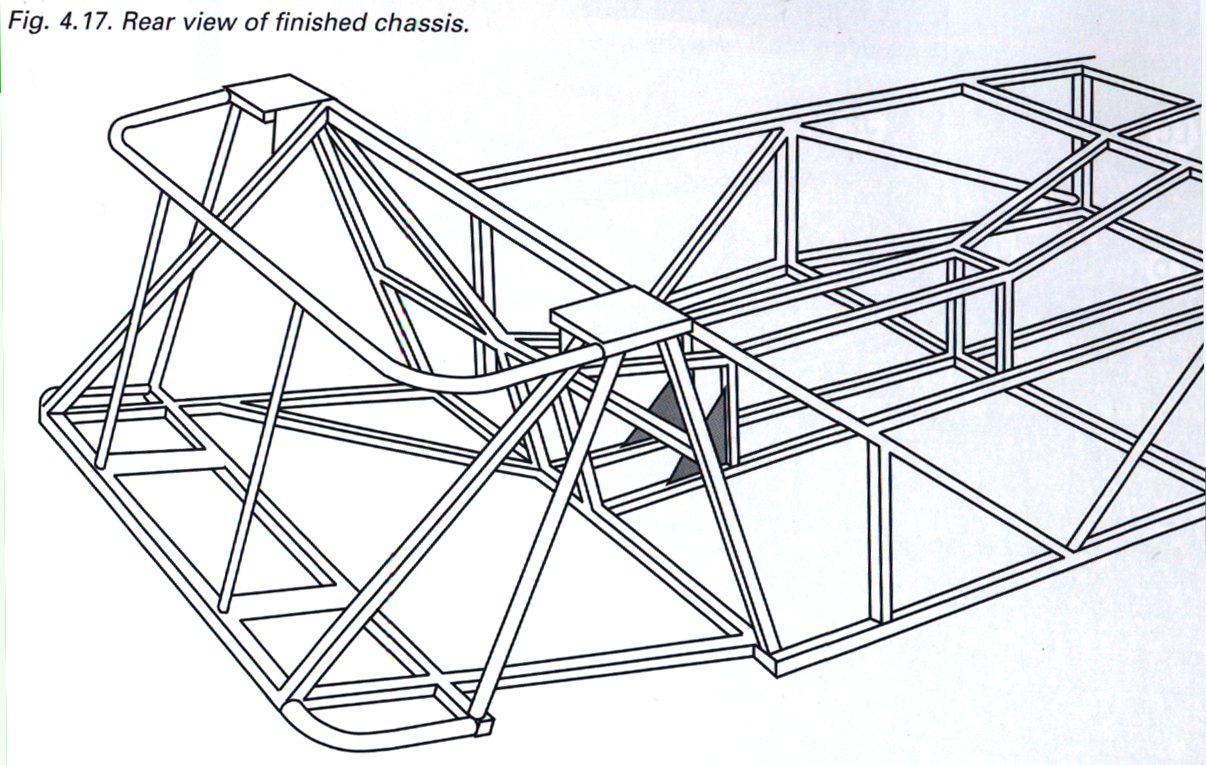







will be copying this transmission tunnel
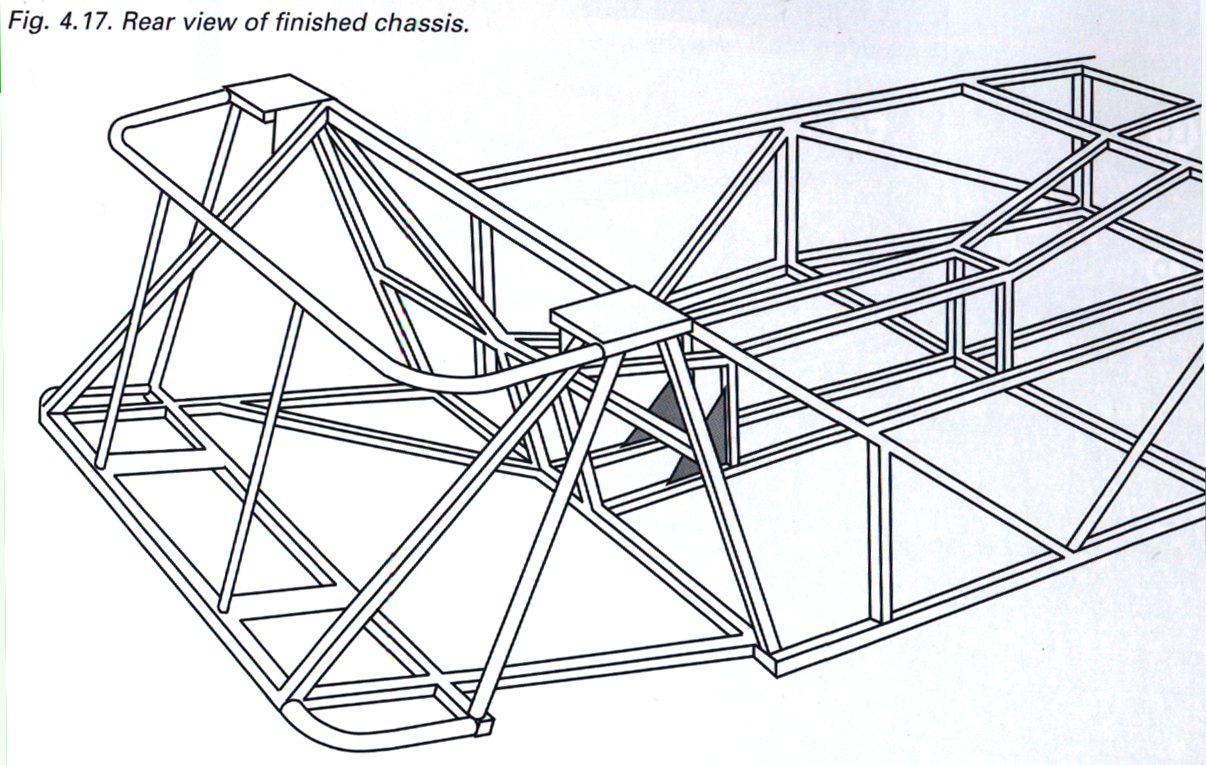
Here's the new new new floor plan, as of 8:35 PM (it seems to change every other hour)...
Side view (suspension mounts in red): This shows the location of the floor in relation to the main beams as well as some of the vertical reinforcement. I have excluded the transmission tunnel in this drawing because I am only focusing on the floor at the moment. That said, the transmission tunnel will connect to the frame at the front end and the roll bar at the rear.

Top View (suspension not included): This is the amount of structural reinforcement I felt was necessary after looking over several pictures of Caterham 7 frames. On this picture you can see where I will attach the transmission tunnel to the roll bar, coming off of the low point of the double hoop all the way down to the back of the tunnel.

Please chime in if you have experience with this stuff, as I'm just going off pictures for now. I'm worried about the roll bar bending due to pressure from the rear springs but I'm not sure if this is worth fretting over.
As of now all floor tubing is 1.5" x 1.5" x .095" square steel
DOM supports for roll bar and suspension reinforcement are 1.5" x .120"
Thoughts and feedback greatly appreciated!
Spence
Side view (suspension mounts in red): This shows the location of the floor in relation to the main beams as well as some of the vertical reinforcement. I have excluded the transmission tunnel in this drawing because I am only focusing on the floor at the moment. That said, the transmission tunnel will connect to the frame at the front end and the roll bar at the rear.

Top View (suspension not included): This is the amount of structural reinforcement I felt was necessary after looking over several pictures of Caterham 7 frames. On this picture you can see where I will attach the transmission tunnel to the roll bar, coming off of the low point of the double hoop all the way down to the back of the tunnel.

Please chime in if you have experience with this stuff, as I'm just going off pictures for now. I'm worried about the roll bar bending due to pressure from the rear springs but I'm not sure if this is worth fretting over.
As of now all floor tubing is 1.5" x 1.5" x .095" square steel
DOM supports for roll bar and suspension reinforcement are 1.5" x .120"
Thoughts and feedback greatly appreciated!
Spence
This is a great build, and way further than I would've got in my senior year of metal shop. I do have a couple thoughts...
I don't have any first hand experience with a caterham frame (yet) but I see a big difference between their frames, and yours. Two giant pieces of metal on either side of the chassis. What you have is essencially a muscle car frame at this point. I'm not sure what your plans are to stop the twisting, but without major bracing and distribution of load, you'll have a mucsle car, not a sports car like the caterham. The whole side of the Caterham is essenitally a section of your solid frame, every piece is designed to share tortional forces with another piece, making the whole car very ridgid. I know there's only so much you can do when you have to tie two subframe together, but if nothing changes you will be hugely disappointed when you get to your first corner.
If you add some of the same metal you used for the frame in an X brace across the floor, you'll greatly decrease the amount of twisting flex between the front and rear axles.
If I were you I'd find a program to run your frame idea through, and see how much it twists. And by twist I mean the ability to lift one corner of the frame up (say the rear right) without the other 3 corners being affected. If you don't do any other bracing, the roll bar will bend from the forces put on it from the suspension and twist in the frame.
I don't have any first hand experience with a caterham frame (yet) but I see a big difference between their frames, and yours. Two giant pieces of metal on either side of the chassis. What you have is essencially a muscle car frame at this point. I'm not sure what your plans are to stop the twisting, but without major bracing and distribution of load, you'll have a mucsle car, not a sports car like the caterham. The whole side of the Caterham is essenitally a section of your solid frame, every piece is designed to share tortional forces with another piece, making the whole car very ridgid. I know there's only so much you can do when you have to tie two subframe together, but if nothing changes you will be hugely disappointed when you get to your first corner.
If you add some of the same metal you used for the frame in an X brace across the floor, you'll greatly decrease the amount of twisting flex between the front and rear axles.
If I were you I'd find a program to run your frame idea through, and see how much it twists. And by twist I mean the ability to lift one corner of the frame up (say the rear right) without the other 3 corners being affected. If you don't do any other bracing, the roll bar will bend from the forces put on it from the suspension and twist in the frame.
-
- Posts: 10719
- Joined: Feb 12, 2006 12:00 PM
- Location: CHI, IL
I agree with the above post. We went through this at the beginning; you will need to triangulate your floor because you don't have much in the way of vertical supports. Also, I'd want direct support for the higher points of the roll bar. A bent, unsupported hoop is not very strong.
If you must go with the double-hoop look for aesthetic reasons, that's fine, but build them out of two inverted-U bars rather than one double-U bar, and support the legs of those inverted U's with extensive bracing.
The last point is the rear suspension support. Can you post another image showing how you're incorporating the diff mount to the body? I'd think you could tie that mount into the shock tower tops to have a support in multiple planes. Maybe you're doing that already and I can't tell.
-tammer
If you must go with the double-hoop look for aesthetic reasons, that's fine, but build them out of two inverted-U bars rather than one double-U bar, and support the legs of those inverted U's with extensive bracing.
The last point is the rear suspension support. Can you post another image showing how you're incorporating the diff mount to the body? I'd think you could tie that mount into the shock tower tops to have a support in multiple planes. Maybe you're doing that already and I can't tell.
-tammer
Here is a representative image of what I'm imagining for your rear suspension mounts:
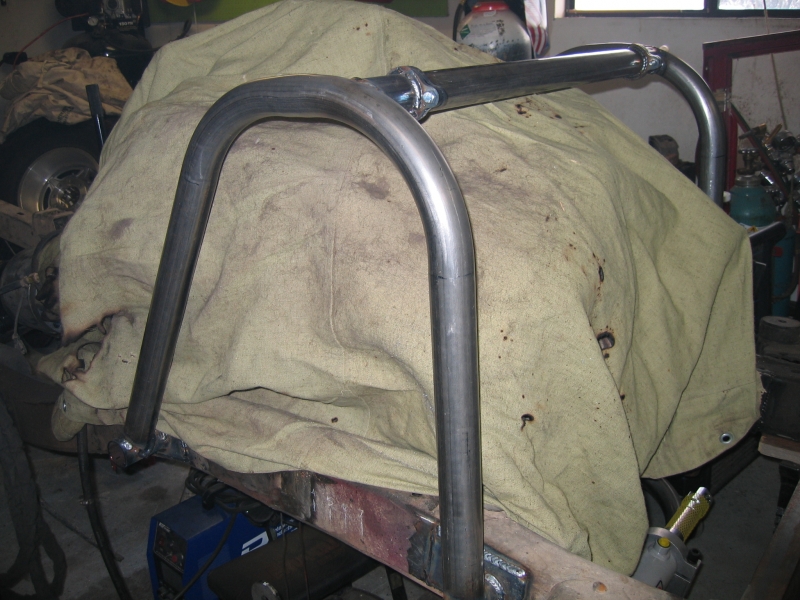
The above is built for a truck, so yours will be different, but it should work well. This hoop design is a simple, proven design. The rear suspension mount you show above will not work well. Your roll bar should be a roll bar, not a mounting point for components and suspension.
You need to have triangulated sidewalls both for safety and for rigidity. Tammer mentioned a good rule of thumb. Try to never have an unsupported bend in a tube structure.
Edit:
You can see the hoop and cross brace in this chassis:

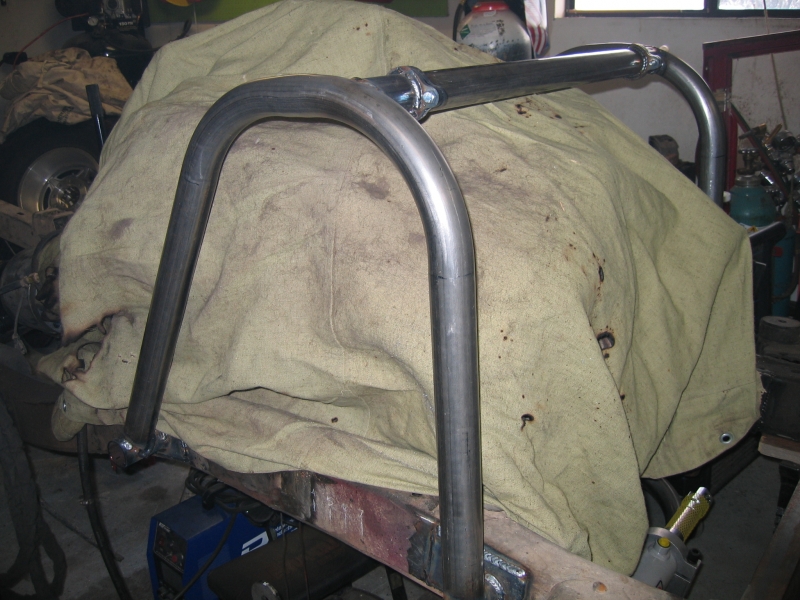
The above is built for a truck, so yours will be different, but it should work well. This hoop design is a simple, proven design. The rear suspension mount you show above will not work well. Your roll bar should be a roll bar, not a mounting point for components and suspension.
You need to have triangulated sidewalls both for safety and for rigidity. Tammer mentioned a good rule of thumb. Try to never have an unsupported bend in a tube structure.
Edit:
You can see the hoop and cross brace in this chassis:

tsmall07 wrote:Here is a representative image of what I'm imagining for your rear suspension mounts:
The above is built for a truck, so yours will be different, but it should work well. This hoop design is a simple, proven design. The rear suspension mount you show above will not work well. Your roll bar should be a roll bar, not a mounting point for components and suspension.
You need to have triangulated sidewalls both for safety and for rigidity. Tammer mentioned a good rule of thumb. Try to never have an unsupported bend in a tube structure.
Edit:
You can see the hoop and cross brace in this chassis:
Thanks for the constructive criticism everyone. I started drawing the full frame in CAD today so I don't have to keep trying to describe everything with 2D pictures and words. I saw the hoop posted above, I understand it, but I dont know where to put it on my car. The seat is literally at the very end of the main tubes, with the top of the headrest directly above the rear subframe mount, if not behind it. My main issue is finding space behind the seat to set up a strong enough suspension mount. Worst comes to worst, I could add some material in between...

The sides look good, but you will still need more bracing in the floor and at the back under the roll bar, making sure the roll bar isn't the only major piece holding the shocks together. That twisting will still happen with the design you have there.
Aside from needing that extra stuff in the floor, it looks good, keep up the great work!
Aside from needing that extra stuff in the floor, it looks good, keep up the great work!
-
- Posts: 10719
- Joined: Feb 12, 2006 12:00 PM
- Location: CHI, IL
The issues I see:
1) The roll hoop is weak. One long bar in a plane with 3 huge bends in it is not strong enough. Also, the only supplementary support for the roll hoop are two bars going forward and down out of the plane of the hoop. Bad. I assume you are bolting the subframe and mounts to the rear part of the main frame beams where they kick up, right? If so, you'll need a chassis structural member connecting those points. That will be in the plane of the roll hoop, and you can make your two roll bars as I described before: two inverted U's that terminate on that straight beam. Then you can connect the two with a decorative piece if you want, and from those attachment points you can add the two supplemental forward-and-down support bars you show.
2) Still no diff mount design. How are you going to support that? I would connect that with the main frame in two directions, and also to the rear shock mount area. The rear suspension upper mounts need diagonals going down to the diff mount, making a full X. Even so, I'm still a little wary of the rear suspension having support to the front only. Have you calculated what the loads into those upper mounts will be?
3) Squares in the floor need diagonals.
This is starting to look good overall, but there are a number of small things you should continue to think about.
-tammer
1) The roll hoop is weak. One long bar in a plane with 3 huge bends in it is not strong enough. Also, the only supplementary support for the roll hoop are two bars going forward and down out of the plane of the hoop. Bad. I assume you are bolting the subframe and mounts to the rear part of the main frame beams where they kick up, right? If so, you'll need a chassis structural member connecting those points. That will be in the plane of the roll hoop, and you can make your two roll bars as I described before: two inverted U's that terminate on that straight beam. Then you can connect the two with a decorative piece if you want, and from those attachment points you can add the two supplemental forward-and-down support bars you show.
2) Still no diff mount design. How are you going to support that? I would connect that with the main frame in two directions, and also to the rear shock mount area. The rear suspension upper mounts need diagonals going down to the diff mount, making a full X. Even so, I'm still a little wary of the rear suspension having support to the front only. Have you calculated what the loads into those upper mounts will be?
3) Squares in the floor need diagonals.
This is starting to look good overall, but there are a number of small things you should continue to think about.
-tammer
Thanks a lot for the tips guys, I really appreciate it. The frame is saved on Daniel's computer so I can't update it here at school, but I have noted to reinforce the floor, create a dif mount, and deal with the roll bar. Regarding that, I will be changing to 2 separate "U's" that intersect at some point (would it be really bad if I wasn't able to intersect them?). Both will terminate on a flat beam in the back; I will include another beam going across the raised portion of the rear, right before the subframe mounts. The roll bar is currently sized at 1.75" x .095", however I could increase that size up to 2.00" x .095 for added safety and rigidity. Sounds like it's a good thing it hasn't been built yet. My main probem, as I have previously voiced, is that the backs of the seats go behind the lower portion of the roll bar (it's mounted at a slight angle). I have no means of supporting it from behind this point as the rear subframe is the only thing from the roll bar back. That's the problem with the rear suspension pickup points as well; I have no means of supporting them other than from the front. That said, I would think that the design I have now with an improved roll bar would do the trick? Lastly, I will try to tie it in better to the transmission tunnel, but I'm sort of at a loss as to how. Thanks again everyone