I was just thinking about adding to this thread, and timely since my most recently completed project (well, 95% at this point) is in the same vein as sail_or_drive's: Storage. This whole pandemic thing has been a mixed bag: while we are forced to say home when not working (it’s not like we went out much anyway), work has been kind of the opposite. It’s been one of the only times where the economy and labor down-turn hasn’t affected the construction industry (at least here in SoCal). So while I see a mounting list of house projects that need my attention, and the perfect soci-political opportunity to tackle them, I’m chained to my PC working on 3 projects at once.
As typical with me, I just can’t seem to stop making work for myself and it seems that owning old cars and an old house just enables that trait; both are in constant need of something. Take for instance one of my two closets in my house.
My company occupies the larger of the two bedrooms in my house and it has the larger of the two walk-in closets, this closet does the heavy lifting for a lot of both personal and business storage. (The closets are a bit of an anomaly for a house of this vintage, 1927, both actual walk-ins, with windows.) We really haven’t done much with the Office and its’ closet since we moved into this house 21 years ago and it has been showing. This whole project started with me needing to repair the plaster ceiling that had popped off the wood lathing underneath it (it was actually a half-assed drywall repair patch from an obvious roof leak long before we bought the house) and, as typical with me, mission creep set in and my task list got a lot longer.
Given the size of the closet, 64”x77”, over half of it was dedicated to file storage with shelving above it. We have/had two metal flat file cabinets for decades that we’ve been dragging around with us first from apartment to apartment and then finally to this house. They house some work files, a lot of old school stuff, photo prints and a vast poster collection (I grew up in an analog world, so paper is the bane of my existence). The big one is the largest they make for 36”x48” media with a footprint of 42”x54”, the smaller one for the smallest standard of 24”x36” and has a footprint of about 30”x40”. It has always been a challenge to find a place to put these, especially that larger one. Once you find a place, they tend to stay there forever since moving them is a royal PITA (empty contents, remove drawers, move carcass, rinse and repeat). So, when I found that these things fit in that closet (barely), in they went and there they stayed. 21 years of life built up around them: clothes, office supplies, X-Mas wrapping, pillows, bowling balls, etc. You get the idea. All that made the closet rather intolerable and unmanageable. The other major “job” for this closet is to house my company’s computer file servers. This has evolved from varying sized towers with attached NAS drives to the recent iteration of three NAS drives. Since we do not have AC in this house (we live on the Westside at a reasonable distance to the ocean so we have a pretty mild climate except for a few weeks of the year), this closet gets pretty warm; I needed to address some air circulation issues at the very least when opening the window isn’t an option.
So, when the failing ceiling became too much to ignore anymore, I got to planning the project. Planning is my thing, I seem to live for it. Whether if be a car project (see my Front End Overhaul thread for that proof) or a house project. I have countless running spreadsheets, CAD files, task lists, etc. for every project I have past, present and future. So I toiled over designing every aspect of this closet with many variations of cabinets and shelving and their arrangements until I got one that worked (it’s surprising how many variations you can come up with for a space this small). I was supposed to execute this project back in March and April when work was slower, but I pulled a muscle in my shoulder bad and pinched a nerve in my neck that wreaked havoc on my life for the better part of 2 ½ months. (Ironically, I injured myself prepping for this project by trying to move replacement metal flat file cabinets that I picked up off Craigslist; more on them below. Getting old sucks, avoid if possible). So, it moved down calendar until last month when work was busy. Naturally.
The first part was to empty the contents and purge. Purging feels good. Really good. It is best done when you’re in a total objective state of mind and back a trash can up to the door and just toss. One trash can, one recycle bin and a large pile of donation stuff later I had the contents pared down to the essentials. (I have no real pictures of what this closet looked like before these few here, but trust me it was rather embarrassing at how bad it looked. I suspect we all have closets like this, so use your imagination).
I then set about procuring the needed supplies and materials namely two new metal flat file cabinets. Since most of my poster collection and other media could be in a smaller cabinet, I started looking for the mid-sized cabinets (these are designed ostensibly for 30”x42” media) which are about 6”-8” smaller in both dimensions than the largest ones. I already had another of the largest cabinets in the garage shop handling the bulk of the company’s files, so it was there for anything I had that was larger than could fit in the new smaller cabinets. Turns out that there is an abundance of metal flat files out there on the used market since most every Architect, Engineer, Designer etc. has gone digital. There are warehouses full of these things selling for pennies on the dollar compared to new. Most are older ones from the ‘70’s and are tanks compared to the flimsier new ones (not unlike the E28 vs. anything newer). In January I found a pair of Hamilton Manufacturing cabinets (built in Two Rivers, Wisconsin) from the early ‘70’s on Craigslist that belonged last to San Diego State University, out in the boondocks of Beaumont (about 92 miles east of here).
Best part about these was that one of them was the rarer 10 drawer version (usually they are only 5 drawers). The smaller drawers worked out better for organization of the posters, so I was jazzed.
The price was fantastic also (about $200/ea.) and after some consternation about how I was going to get these home, the seller offered to deliver them for another $70. Awesomesauce. The other items like a new light, an exhaust fan misc. hardware was all on a list and ordered at the appropriate times.
The exhaust fan was an addition to help with any excess heat gain from the servers (however since switching from the tower PC to the NAS’s the heat output was cut radically) and general air circulation to avoid dust, mold and/or fungus (old paper you know).
So, after more design fine tuning of the cabinetry & shelving to better organize the crap going back in, I bit the bullet and scheduled it to start Memorial Day weekend (it’s not like we were going anywhere). The big disadvantage to moving this down calendar to now was back in March/April I was planning on just plowing through the whole project in 10-14 days, but work in May/June made me change that to a weekend-only project. That prolonged the whole closet displacement experience which was felt in several rooms of the house and the garage shop (and by extension my back yard).
Relocating the clothes wardrobes & coats to a temporary rack in the bedroom, setting up the servers on my desk in the office and emptying the existing flat files (transferred to the other flats in the garage shop) were on the first weekends’ agenda.
Next few weekends were demolition to remove the existing cabinetry & flat files and rough Electrical for the light, exhaust fan and switches (the closet only had an old-school pull chain incandescent exposed bulb). The existing small casement window needed refinishing also.
Once all that was done, it was time to repair and/or replace the plaster ceiling. I was prepared to do this myself; how I had no idea since:
A. I hate drywall work
B. I had no way of transporting several sheets of drywall
C. It’s a small space and all the work is overhead working around upper shelves
D. I’m terrible at drywall and more to the point coating and finishing it
E. Did I mention I hate drywall work? Mostly because I’m pretty bad at it.
After a few calls to some contractor contacts I lined up “A Guy” to stop by one week to take care of it. He even did the demo of the existing plaster ceiling. Best cash payment I made on this project.
In the meantime while the drywall was being scheduled and done, I got busy in the shop making sawdust. I am at best a pro-hack when it comes to woodworking and while being a life-long passion of mine, I am more of “production” level kind of cabinet maker. Meaning that most of what I make is pragmatic and purpose-design & built cheaply and efficiently. I learned long ago how to dovetail joints and hand plane exotic woods, but most everything I make is far from that (in fact I’m sure I’ve forgotten how to do that stuff now); paint grade or birch plywood is more my speed these days.
So after (more) CAD layouts and planning I got my cut lists and headed off to my favorite local lumber house: Anderson Plywood in Culver City nearby. Damned few of these old-school shops left these days, you know the ones housed in a hundred year old bow truss warehouse, racks of plywoods of all colors and flavors, more racks of exotic hardwoods and veneers, and most importantly: people who know what they’re doing and talking about.
One of the greatest thing about Anderson is for a modest price, they will mill down the plywood stock all you want, which is good since it was the only way 3 sheets of ¾” plywood was fitting into the CR-V to get it home. Anderson is a hopping place at any given time and not open on Saturday, so there are waves of cabinet makers, finish carpenters and guys like me jockeying for the few loading spaces and lining up for milling (all of whom laugh at me shaking their heads when I show up in the Honda and look at all that plywood; I love proving them wrong when it all goes in. With room to spare.). They had a deal on pre-finished Birch ply so that cut my workload in half but did change up my finish strategy. I think it was for the better going from paint to natural wood. (Seriously for the additional $10/sheet, I couldn’t have bought the amount of polyurethane needed to do all that, let alone the time.)
The big problem with too much crap in ones’ life is space is a zero-sum game, if you’re not diligent about culling and organizing, you pay down the line for your laziness. The shop in my garage is a prime example of this; I spent the better part of a day clearing out space just to get to the centerpiece of this shop: My JET 10” cabinet table saw
This and the outfeed benches attached to it were to be instrumental in me completing this project. After some much needed tune-up, cleaning and waxing the table, the saw was ready for primetime. First weekend was milling down all the panels and pieces to final sizes:
I had two equipment drawers that I was reusing from the previous closet setup, so that ended up taking a fair amount of time to get it all sorted out (in the end it was still off a little; oh well like I said: I’m still an amateur).
Back inside, now that the plaster was finally dry, it was time to paint. After a few weekends in between shop time, the room was finally done with its’ primer and two final coats:
After some milling and installing of some Red Oak edge strips, I was ready to go for the first round of cabinet installation:
Flat files in first; this required some physical labor assistance as even the empty carcasses still weigh a bunch not to mention really cumbersome. (Thanks, Phil).
Followed by the tops and shelves and a new server rack:
Fitting the drawers and rack and adjusting them to work took the better part of the whole next day, but finally:
Final installation of the fan, light and window shade happened in there somewhere
All that was left was to move everything back in. I almost hated to do that since we were getting used to that room being nice, neat and clean; it almost never looked this good.
That was all up to last weekend. Just a few items left to figure out and complete, namely some paper and board supplies and putting the weatherstripping to that window (which is all part of my on-going exterior door & window rehab, which never seems to be done.) The only other item is an on-going re-organization and cataloging of the poster collection, but that seems like it will take the rest of my adult life.
I know, it’s only a small closet, right? Why I am going on about such an inconsequential thing; but in life you have to celebrate the little things or you’ll go mad. And in today’s world right now, this is a big victory.
Cheers.
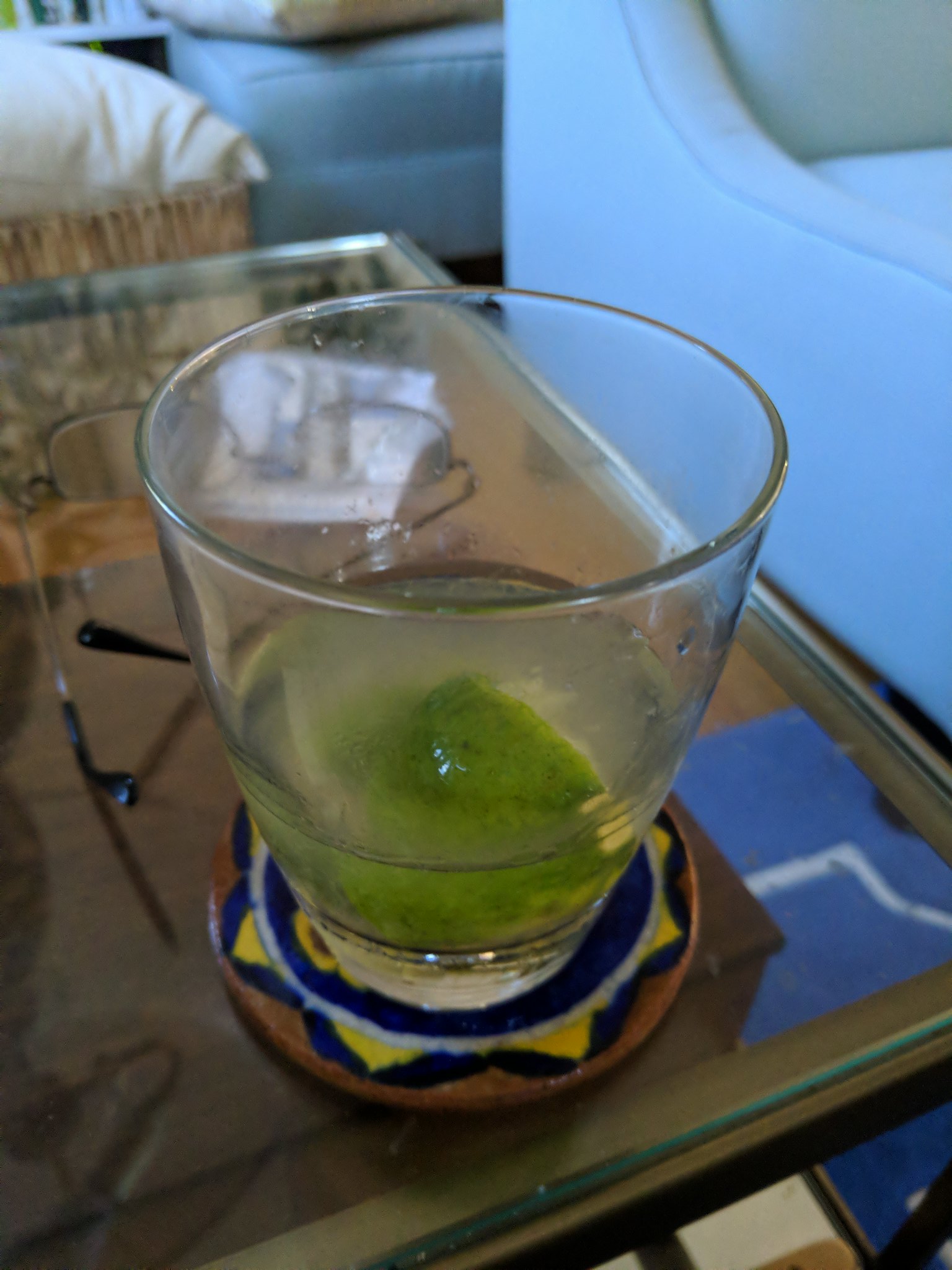