Page 16 of 25
Posted: May 06, 2011 4:44 PM
by tsmall07
You "can't" brace the rear mounts to the rear because your frame terminates into the subframe mounts. I would have had the subframe mounts off to the side of the frame and extended the frame rail beyond the subframe mounts. That would make your life much easier and would solve all of your issues. It would require some cutting and rewelding, but that's what it's all about.
Your "double U" roll bar pieces don't have to intersect. It would be easier to make complete U shapes and bring both all the way down to the cross member. Weld them together with steel straps.
Posted: May 06, 2011 5:25 PM
by sbeckman7
Thanks, working on it now

Posted: May 09, 2011 8:49 PM
by sbeckman7
Quick update: Should have the updated frame finished in Inventor by tomorrow, along with a lead on how to get the program at home again as my old student copy expired. Also picked up 2 (not one but TWO) extra struts from wickahead (who also helped with the Autodesk software), so thanks a million for that Mark!
Posted: May 10, 2011 7:39 PM
by sbeckman7
Posted: May 10, 2011 8:15 PM
by mtnman533
It looks 100% better than it did. One last thought is that the roll bars really have nothing to stop them buckling from hitting at a funky angle (like if the car landed on one side of one). So it may be a little overkill, but I would do it anyway just for piece of mind.
What I think needs to be done to make this as good as possible, I'm sure others have ideas as well. Just a simple X in both those big gaps behind the seat (I realize movement of the seat is needed) would greatly decrease the likeliness of those bars buckling. Just something to think about.
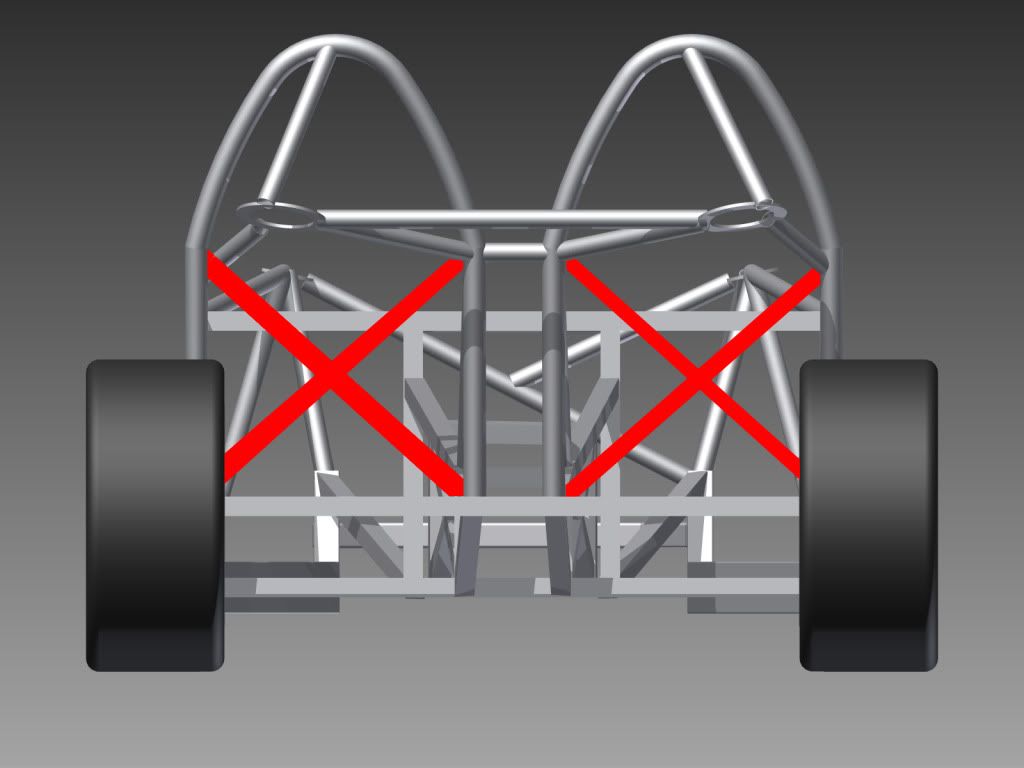
Posted: May 10, 2011 9:27 PM
by sbeckman7
Hmm not a bad idea. The seats will pass under the roll bars to some extent so that's why I havent put any X piping in between them, but I could always bend them at the ends to curve them out and give more room. Thank you sire
Posted: May 11, 2011 12:20 AM
by Tammer in Philly
sbeckman7 wrote:Hmm not a bad idea. The seats will pass under the roll bars to some extent so that's why I havent put any X piping in between them, but I could always bend them at the ends to curve them out and give more room. Thank you sire
Sire? I didn't realize mtnmn was a king ...
I'd try to keep the seat and most importantly, the driver's head in front of the plane of the roll bar. I do like the idea of supporting the hoops. Agree that this is very much improved. If you have the diff mount where I think it will go, with a large "V" running out and up to the shock mount support and bars going forward to the node where the small bar connects your two roll hoops, you should be in pretty good shape.
-tammer
Posted: May 11, 2011 12:36 AM
by mtnman533
I'm too poor to be a king

.
I agree with tammer that keeping the head/seat in front of the roll bar is a good idea.
Posted: May 11, 2011 12:38 AM
by sbeckman7
You could say I'm bringing Ye Olden English back.
Just noticed I forgot to post these pics I took of the seat/roll bar layout last week. These might help. The tape measure is at 35" and represents the mounting postion of the roll bar, although it is not angled as the actual bar will be.
The mounting location
angled back by my hand; with the roll bar angled as well this should work out nicely.
Untilted side view. This is more or less where the seat will be mounted.
Tilted side view

Posted: May 11, 2011 7:08 PM
by sbeckman7
So if I tilt the roll bar another 5 degrees, for a total of 15, I should have enough space for the seats in front. I finished the diff mount in CAD but didnt have time to finish moving the roll bars back, so I'll get it done by friday.
Posted: May 12, 2011 4:55 PM
by sbeckman7
Posted: May 12, 2011 5:03 PM
by tsmall07
I think it's finally time to ask this question. Tammer and I have been talking about it and waiting for you to decide, but I haven't seen it.
Where is your fuel tank going?
sbeckman7 wrote:but I could always bend them at the ends to curve them out and give more room.
You should never put bends in a structural member if you don't absolutely
have to. If you do, the bend needs to be supported. The X behind the seats will not be as rigid if it is not in the same plane as the roll hoop.
It
is starting to look pretty good. I guess you decided not to extend the frame rails.
Posted: May 12, 2011 5:51 PM
by sbeckman7
The fuel tank will go behind the seats. I'm shooting for around a 15 gallon tank. I think I'm going to get a cylindrical tank that I can put right behind the roll bar. Good point though.
Regarding extending the frame, do you guys think it would be okay to just weld some more material in? I know it wouldn't be as strong as it is now, but it would still be fine right? It'll just make my life much easier trying to find space for my feet.
Posted: May 12, 2011 6:38 PM
by tsmall07
sbeckman7 wrote:
Regarding extending the frame, do you guys think it would be okay to just weld some more material in? I know it wouldn't be as strong as it is now, but it would still be fine right? It'll just make my life much easier trying to find space for my feet.
What are you talking about? I was talking about extending the rear of the frame to brace off the rear strut mounts to the rear. You may not need it now, though.
Posted: May 12, 2011 6:40 PM
by sbeckman7
Oh, yeah I think it's fine. But could I theoretically add some material, say 4" in my frame? Like cut it in half, add more, and then re-weld it?
Posted: May 12, 2011 10:26 PM
by Tammer in Philly
sbeckman7 wrote:Oh, yeah I think it's fine. But could I theoretically add some material, say 4" in my frame? Like cut it in half, add more, and then re-weld it?
Now that you have the horizontal boxed member at the back of the frame, you might not need to extend the frame rails back for additional support. I think the bracing from the shock mounts to the diff mount should suffice.
Think hard about fuel tank placement, support (you want it protected), and pump/line configuration. Where will you run the lines? How will you protect them?
Keep up the progress. The frame is starting to look really good. You've now got a car I wouldn't be scared to climb into. :-)
-tammer
Posted: May 12, 2011 10:36 PM
by sbeckman7
Tammer in Philly wrote:You've now got a car I wouldn't be scared to climb into. :-)
-tammer
High praise right there! So I think I may add about 4 inches in the overall length by cutting the frame rails in half and adding some material. Benefits include greater stability and not having to amputate feet beforehand.
Posted: May 12, 2011 11:41 PM
by rmiddendorf
sbeckman7 wrote:Tammer in Philly wrote:You've now got a car I wouldn't be scared to climb into. :-)
-tammer
High praise right there!...
That's like x100 coming from Tammer. He does know his stuff from what I know of him here on the forum!
Posted: May 13, 2011 5:12 PM
by tsmall07
sbeckman7 wrote:not having to amputate feet beforehand.
That would be optimal. Make sure you bevel the edges of your frame members before you weld them back together. That way, you can be sure you get 100% penetration. This will be a multi-pass weld. The root pass is most important, so don't screw it up.
I was thinking about it last night, and I think you should add a horizontal hoop or two off the back of the thing to provide some rear impact protection. This will help protect you and your fuel tank. Getting hit by a car from the rear or going backwards into a tire wall/ARMCO would not end well as it sits right now. You could also tie this into your diff mount and have kickers down from the top of your roll hoop.
Posted: May 13, 2011 5:51 PM
by sbeckman7
tsmall07 wrote:
I was thinking about it last night, and I think you should add a horizontal hoop or two off the back of the thing to provide some rear impact protection. This will help protect you and your fuel tank. Getting hit by a car from the rear or going backwards into a tire wall/ARMCO would not end well as it sits right now. You could also tie this into your diff mount and have kickers down from the top of your roll hoop.
Beveled surface noted on the weld, thanks. That's an interesting idea on the rear "bumper". I don't know why I didn't think of something like that beforehand, but I'll see how the rear end looks once the rest is done. I'm thinking it may be alright with the beefy diff mount and what not. Anyway, did the weight calculations today and the results are looking really good. I won't bother including all the individual piece lengths in here, but I checked every length using my CAD drawing. Here's what I got:
Metal Length/Weight estimates based on 1.5” x .095” DOM round tubing (1.426 lbs/ft), square tubing estimated at 1.815 lbs/ft, 1.75” x .095” DOM round tubing (1.679 lbs/ft), 2”x 4”x .120” Rectangular Steel estimated at 4.695 lbs/ft
Total Square Length: 923.75”
Total Round 1.5” length: 883.5”
Main Frame Rails total length: 205.37”
Total Roll Bar Length: 160"
Square Tubing Weight: 139.75 lbs
Round 1.5” Tubing Weight: 105 lbs
Roll Bar: 23.5 lbs
Shock Mounts: 10 lbs
Main Rails: 80 lbs
Total Frame Weight: 358.25 lbs
my original estimate was 400lbs, so....

Posted: May 13, 2011 6:19 PM
by Tammer in Philly
Tyler has a very good point with rear crush room. Your diff mount might be strong, but it mounts the diff--and therefore locates the half shafts, subframe, driveshaft, etc. If you do get tagged from behind, you want something to take up that impact before you start relocating your entire driveline. Not to mention more material to dissipate energy before it gets to your seat.
I'd consider a design with some gently bent tubes of slightly thinner metal than the rest. This will both save weight and promote crumpling/bending of the non-structural tubes.
-tammer
Posted: May 13, 2011 6:55 PM
by sbeckman7
Tammer in Philly wrote:Tyler has a very good point with rear crush room. Your diff mount might be strong, but it mounts the diff--and therefore locates the half shafts, subframe, driveshaft, etc. If you do get tagged from behind, you want something to take up that impact before you start relocating your entire driveline. Not to mention more material to dissipate energy before it gets to your seat.
I'd consider a design with some gently bent tubes of slightly thinner metal than the rest. This will both save weight and promote crumpling/bending of the non-structural tubes.
-tammer
Sounds like I could integrate the crumple zone tubes into the tubes that will support the body?
Posted: May 13, 2011 7:34 PM
by Tammer in Philly
sbeckman7 wrote:
Sounds like I could integrate the crumple zone tubes into the tubes that will support the body?
Bingo.
-tammer
Posted: May 13, 2011 8:21 PM
by tsmall07
I would go for stronger rather than weaker with the bumper. You can't count on steel tube to crumple in a controlled fashion like a regular car. Once it kinks, it will flatten quickly. A thinner bumper will provide less protection, I think.
Posted: May 13, 2011 11:51 PM
by sbeckman7
Sweet, thanks for the tips guys.
On another note, I just had one of the best Friday afternoons I've ever experienced. I attended the Porsche World Roadshow with my dad at Candlestick park in SF for a 2 hour performance driving course hosted by Porsche. There were about 50 cars in total but our group of about 15 participated in a short autox circuit and then a higher speed 1 mile "track" also laid out in cones in the Candlestick parking lot. I signed up knowing that I was too young to actually drive but Porsche is my favorite car company and I never pass up invitations like this. So my dad drove 8 different porsches and I listened to 8 different porsches. Actually 9. For the track bit I was allowed to ride with an instructor who led the participants around the track in my dream Porsche: a 911 Turbo S coupe. I have never experienced acceleration or grip like that in my life.
So then remembered something: the turbo s has 303 hp/ton and it blurred my vision accelerating and lifted my feet off of the carpet. My car, once completed, will produce somewhere between 350 and 400 hp/ton. So I'm not really sure what I'll end up with, but I know I will be extremely grateful for traction control and keep my right foot light as a dandelion. Just thought I would share my adventures with everyone

Posted: May 16, 2011 6:36 PM
by sbeckman7
Started making the jig for the front suspension today. I widened my friend's e30 strut brace by cutting it in half and inserting a piece of tubing. Since I couldn't weld the steel insert to the aluminum brace, I jammed it in and then put 2 nails though the pipe. I'll attach the strut brace to the camber plates using some mini clamps and then the brace to the frame by tack welds. Also found a place to order metal called Tube Service Co. With 20 ft lengths, I'll have enough spare for errors and was quoted at $220 for 80ft of 1.5"x1.5"x.095" square tubing (1008-1010 alloy) and 80ft of 1.5"x.095" DOM.
Posted: May 17, 2011 9:46 PM
by sbeckman7
Posted: May 18, 2011 7:35 PM
by sbeckman7
Posted: May 24, 2011 1:54 AM
by sbeckman7
Fine tuned the front suspension today by realigning caster as well as lowering the strut towers 1 1/8". I did this by actually cutting the jig I made (part of it, so I would still have an accurate reference) and removing material from the vertical supports. Then I jacked the front of the car up so it was 1 1/8" higher than it will be once it's fully weighted, and re-welded the jig in place. Over the weekend I visited a friend and took a trip to Martinez, CA to find a shop that can make the roll bar. They were closed by the time I got there but I will be going back later in the week.
Lastly, I finally have a job! Working in one of the shops at Infineon Raceway! It's a fabrication place, so I'll be learning to TIG weld while helping out, and getting gas/car money at the same time

Posted: May 24, 2011 2:48 AM
by Tammer in Philly
sbeckman7 wrote:
Lastly, I finally have a job! Working in one of the shops at Infineon Raceway! It's a fabrication place, so I'll be learning to TIG weld while helping out, and getting gas/car money at the same time :)
Sweet! Nice work.
-tammer